Future of Fashion with 3D Printing
- Shraddha Srivastava
- Mar 13, 2024
- 3 min read
Recent statistics reveal that 38% of global consumers express interest in purchasing 3D-printed clothing, showcasing a noticeable surge in curiosity about this innovative technology. This heightened interest serves as a compelling reason for fashion retailers to stay abreast of the latest advancements in 3D printing. The technology not only sparks interest but also offers enticing possibilities for design, customization, and sustainability within the fashion realm.

While still in its early stages, this groundbreaking approach holds enormous potential to transform the conventional fashion industry. Let's embark on a journey into the realm of 3D-printed garments, exploring their origins, the challenges they currently face, and the promising future they portend.
What is 3D Printing?
3D printing, also known as additive manufacturing, is a method of crafting three-dimensional objects from a digital blueprint. Unlike traditional manufacturing techniques involving carving or shaping solid blocks, 3D printing constructs objects layer by layer. 3D printing creates objects by layering materials based on a digital model. It's like building with virtual LEGO blocks, allowing for precise and intricate designs in the manufacturing process.
Who invented 3D Printing on Clothes?
The genius behind the invention of 3D printing on clothes is Chuck Hull. Often called the "father of 3D printing," Chuck Hull paved the way for this futuristic technology with his creation of stereolithography (SLA), the first-ever commercial 3D printing technology. His innovative contributions extend further with the development of the .stl file format, a common language in the 3D printing world today. Thanks to Chuck Hull's groundbreaking work, the fashion industry has witnessed the exciting integration of 3D printing, opening doors to a new era where garments are crafted layer by layer using precision technology.
Challenges of 3D Printing on Clothes:
Despite its innovative potential, 3D printing on clothes is not yet a common sight in everyday wear. Several challenges hinder its widespread adoption:
Material Limitations: The current materials used in 3D printing can be stiff and uncomfortable, making them less suitable for daily wear.
Technology Development: While continuously evolving, 3D printing technology is still under development to ensure both comfort and functionality in everyday clothing.
Cost and Accessibility: Specialized techniques and materials contribute to the higher cost of 3D-printed clothing, limiting its accessibility to a broader audience.
These challenges highlight the ongoing journey towards making 3D-printed clothes more comfortable, affordable, and mainstream. As technology advances, these hurdles are likely to be overcome, bringing the innovative world of 3D printing into the closets of everyday consumers.
3D Printing: A Future Fashion Technology
Iris van Herpen, a Dutch fashion designer, emerged as a trailblazer in seamlessly integrating 3D printing into haute couture. In 2010, she captivated the fashion world with her "Crystallization" collection, a mesmerizing showcase of the first-ever catwalk presentation featuring 3D-printed clothing. These pieces weren't your typical everyday wear; instead, they resembled dramatic, sculptural works of art.
The allure of 3D-printed fashion lies in its ability to transcend the boundaries of traditional sewing techniques. Designers utilize Computer-Aided Design (CAD) software to craft intricate and complex shapes that would be challenging, if not impossible, to achieve through conventional methods.
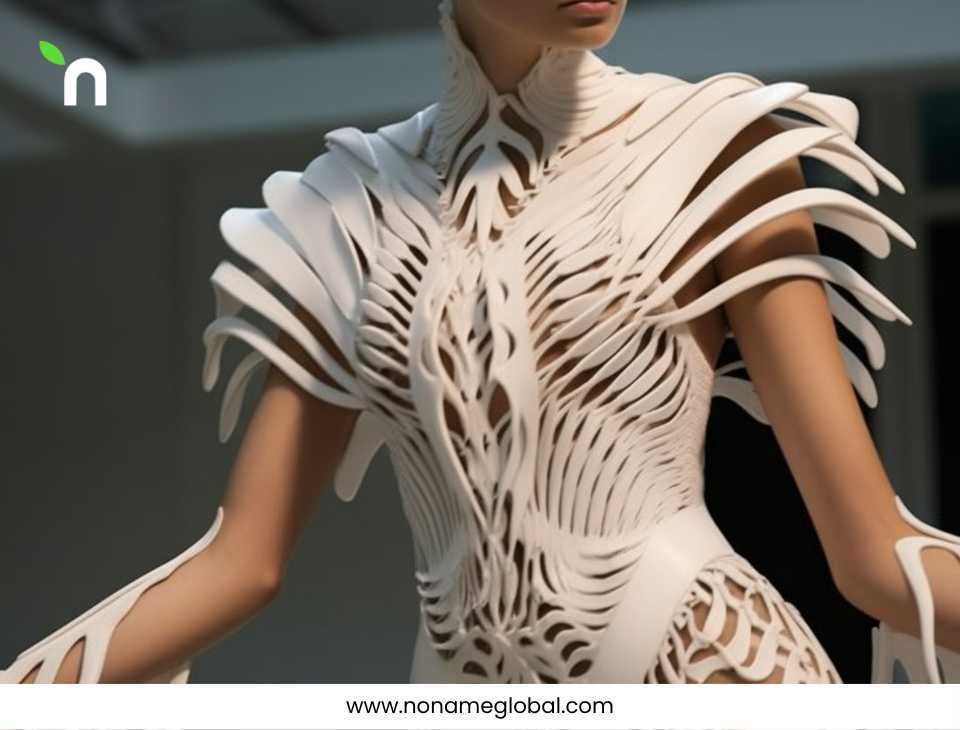
The Future with NoName
In the landscape of clothing manufacturers in India, NoName stands as a beacon of innovation. While 3D-printed clothing is still considered avant-garde, NoName is keenly aware of this technology's potential. As we look towards the future, envisioning a world where 3D-printed clothing is accessible and comfortable, manufacturers like NoName play a pivotal role.
The challenges currently faced by 3D-printed clothes – material limitations, ongoing technology development, and the associated costs – are areas where NoName sees potential. With an eye on the future, NoName aims to integrate 3D printing technology into its manufacturing processes, offering a glimpse into the future of fashion in India.
Conclusion In conclusion, 3D printing on clothes represents a captivating chapter in the ongoing narrative of fashion evolution. Despite current limitations, the trajectory is clear – towards a future where 3D-printed clothing seamlessly blends innovation, comfort, and accessibility. As technology advances and pioneers like NoName lead the way, we may soon witness a transformation in our wardrobes, where the lines between high fashion and everyday wear blur, thanks to the revolutionary embrace of 3D printing.
Embrace the future of fashion with NoName – your trusted partner in clothing manufacturing. Explore innovative possibilities and stay ahead in the ever-changing landscape of the fashion industry. Contact us today to discover how we're shaping tomorrow's trends through cutting-edge technologies like 3D printing.
WhatsApp: +91-9717 508 508
Email: hello@nonameglobal.com
Website: www.nonameglobal.com
Online meeting: https://calendly.com/nonameglobal/meet
Comments